2025 Innovations in Hydraulic Pumps: Transforming Efficiency and Sustainability in Industrial Applications
The hydraulic pump industry is poised for significant innovations by 2025, as emerging technologies and sustainable practices reshape industrial applications. With the global hydraulic pump market projected to reach USD 12.73 billion by 2026, growing at a CAGR of 5.2%, the drive for efficiency and sustainability has never been more critical. These pumps, essential in numerous sectors such as construction, manufacturing, and agriculture, are undergoing transformations that prioritize energy conservation and reduce environmental impact. Advanced hydraulic pump designs are being integrated with smart technology, promising to optimize performance and minimize wastage.
Sustainability is becoming a fundamental objective within the hydraulic pump sector, with recent reports indicating that companies are increasingly focusing on eco-friendly materials and processes. According to a study by the International Energy Agency (IEA), improving the efficiency of hydraulic systems can reduce energy consumption by up to 30%. This urgent call for innovation in hydraulic pump technology not only addresses current market demands but also aims to meet regulatory pressures for greener operations. As we delve into the innovations expected in hydraulic pumps by 2025, it is clear that the future of industrial applications hinges on a harmonious blend of efficiency and environmental responsibility.
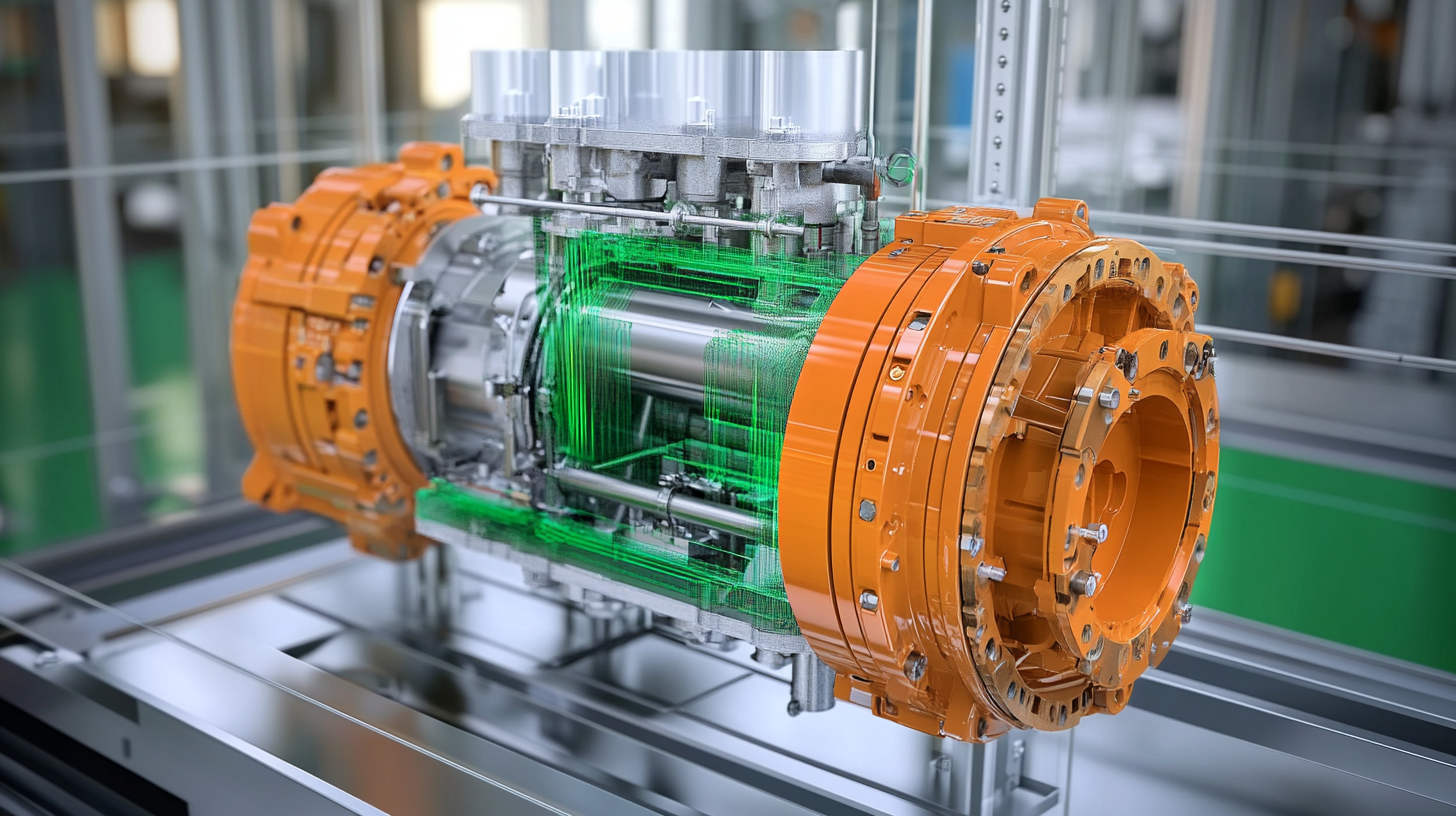
The Rise of Smart Hydraulic Pumps: Integrating IoT for Enhanced Monitoring and Control
The rise of smart hydraulic pumps is set to revolutionize the fluid systems industry, with significant implications for efficiency and sustainability in industrial applications. These advancements are critical as companies strive to optimize energy usage and reduce emissions, aligning with global sustainability goals. A recent report highlighted that smart pumps, equipped with IoT technology, can enhance energy efficiency by up to 30%, a substantial improvement for process industries where every percentage point matters. The integration of sensors into fluid power systems is creating a new landscape of design opportunities. These smart systems enable improved precision and control, allowing operators to monitor performance in real-time. With enhanced monitoring capabilities, companies can identify inefficiencies quickly and make data-driven decisions to boost performance. For instance, smart fluid hydraulics can provide detailed insights into operational parameters, ultimately leading to decreased downtime and maintenance costs. Recent innovations in hydraulic systems, such as those seen in the Caterpillar Excavator and Honda’s hybrid-electric powertrain, further illustrate the shift towards smarter hydraulic applications. The advanced positive flow electrohydraulic systems not only enhance the operating efficiency of machinery but also contribute to overall environmental sustainability. Reports indicate that machinery incorporating such hydraulic advancements can decrease fuel consumption by approximately 15%, showcasing the direct benefits of integrating smart technologies in hydraulic systems. This technological transformation in hydraulic pumps signifies a crucial step towards a more efficient and sustainable industrial sector. As the mobile hydraulic equipment market continues to grow, the demand for these smart, sensor-integrated systems is expected to increase, enforcing a paradigm shift in how industries manage fluid power systems.
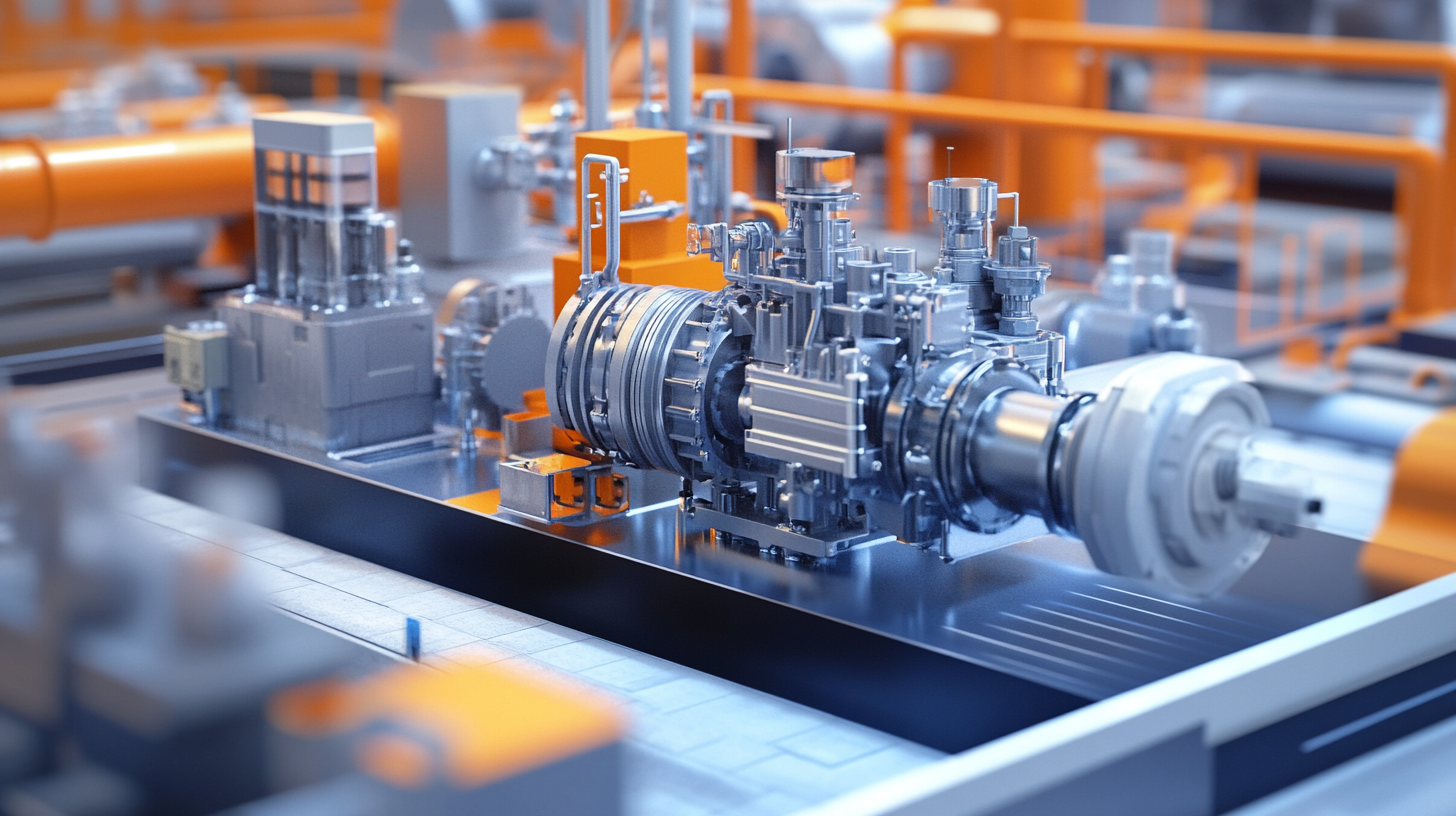
Advancements in Pump Design: Maximizing Efficiency and Reducing Energy Consumption by 30%
The evolution of hydraulic pump design is paving the way for a more efficient and sustainable industrial landscape by 2025. With newly engineered components and innovative configurations, modern hydraulic pumps are now capable of achieving energy consumption reductions of up to 30%. This remarkable leap in efficiency comes from incorporating advanced materials and streamlined designs that minimize friction and enhance performance.
One significant advancement is the integration of smart technology into pump systems, allowing for real-time monitoring and adaptive performance adjustments. These intelligent systems not only optimize energy use but also prolong the lifespan of the equipment, reducing operational costs. Additionally, new designs often explore the use of more efficient hydraulic fluids, which can further decrease energy wastage while improving overall system reliability.
Furthermore, the move towards sustainability in hydraulic pump development is evident through the adoption of eco-friendly materials and manufacturing processes. By focusing on reducing the carbon footprint associated with production and operational usage, manufacturers are not only meeting regulatory standards but also responding to the growing demand for environmentally responsible solutions in industrial applications. This blend of efficiency and sustainability positions hydraulic pumps as essential players in the future of green industrial practices.
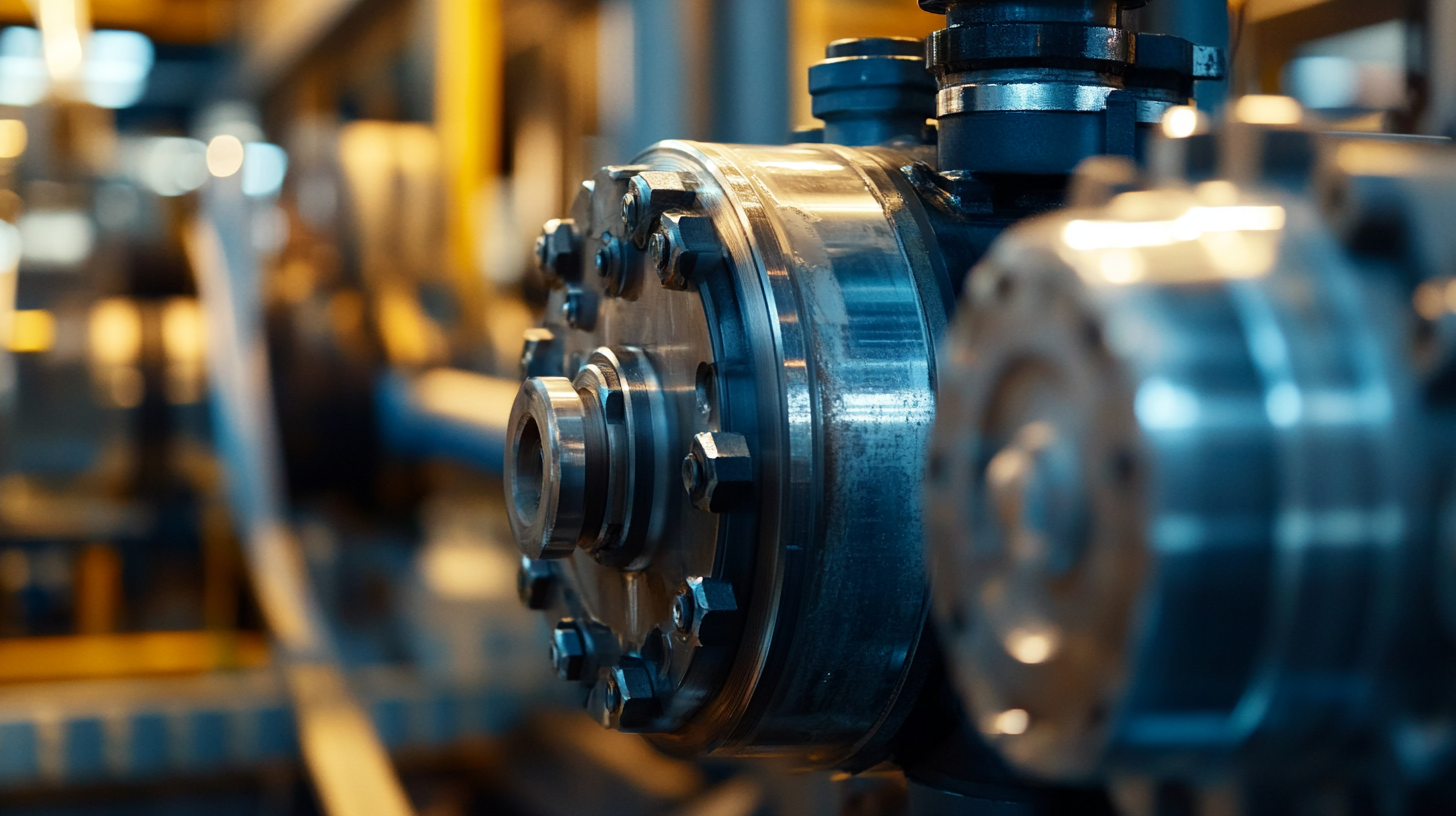
Sustainable Materials in Hydraulic Pump Manufacturing: Reducing the Carbon Footprint by 25%
In recent years, the industrial sector has seen a profound shift towards sustainability, with companies striving to minimize their carbon footprints while maintaining operational efficiency. One of the key areas where this trend is evident is in the manufacturing of hydraulic pumps. By adopting sustainable materials in production processes, manufacturers are not only reducing waste but also lowering their overall emissions by an impressive 25%. This transformation marks a crucial step towards a more environmentally responsible industrial landscape.
Innovations in material science have opened new avenues for creating hydraulic pumps that are both efficient and sustainable. Manufacturers are increasingly turning to alternatives such as bio-based plastics and recycled metals, which offer comparable performance to traditional materials without the associated environmental impact. These eco-friendly options not only help in reducing greenhouse gas emissions but also enhance the durability and lifespan of hydraulic systems, leading to lower maintenance costs and resource consumption in the long run.
Moreover, the integration of sustainable practices in hydraulic pump production goes beyond just materials. Companies are investing in energy-efficient manufacturing processes and technologies that further contribute to overall sustainability. By focusing on the entire lifecycle of hydraulic pumps—from sourcing materials to production, usage, and disposal—manufacturers are paving the way towards an industrial future that prioritizes both efficiency and environmental stewardship. This holistic approach not only benefits the planet but also positions businesses as leaders in a rapidly evolving market that increasingly values sustainability.
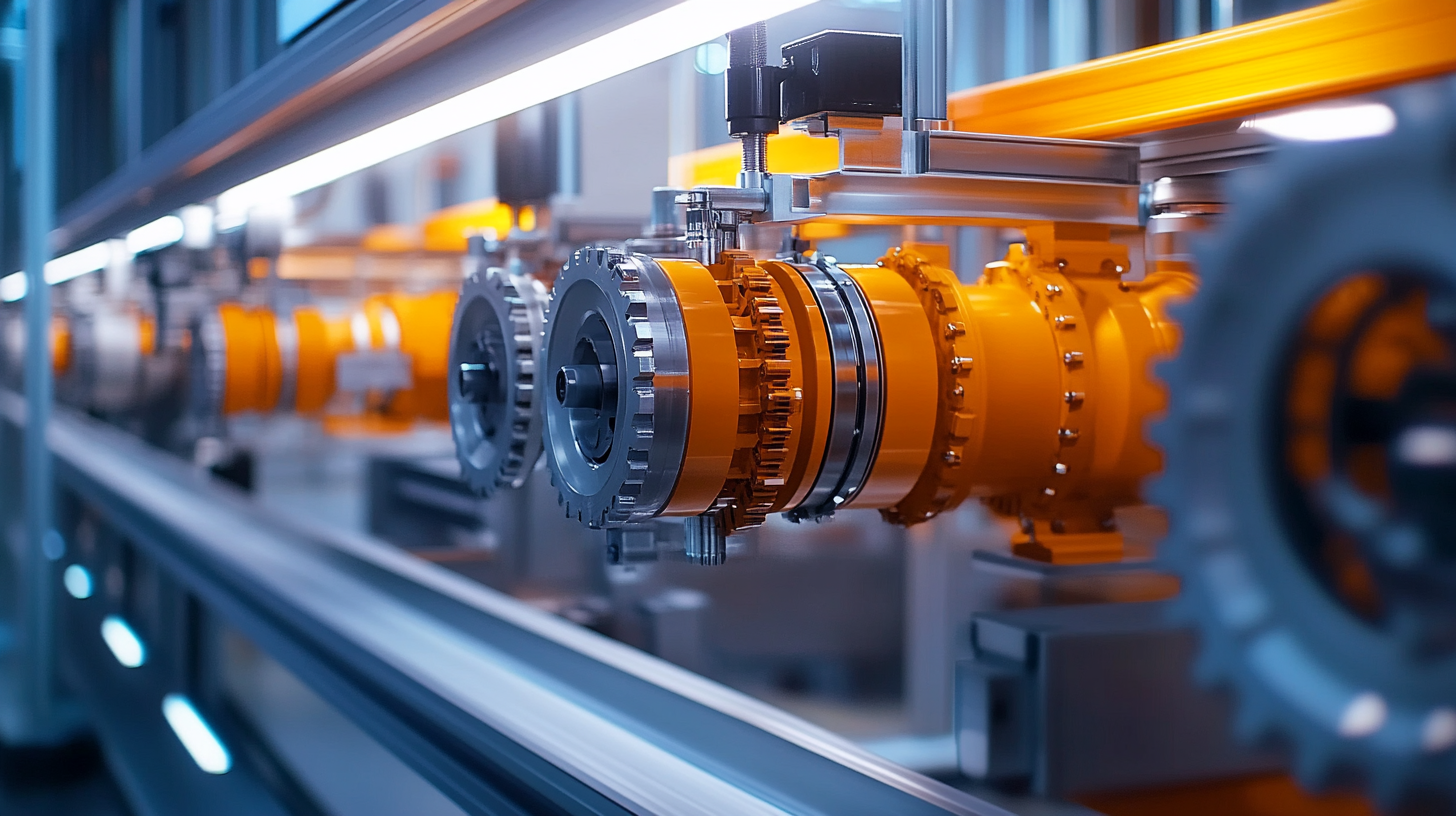
Predictive Maintenance in Hydraulic Systems: Leveraging Data Analytics to Decrease Downtime by 40%
Predictive maintenance has emerged as a pivotal strategy for enhancing the reliability of hydraulic systems, particularly within industrial applications. As industries strive to reduce operational costs and improve efficiency, leveraging data analytics capabilities has proven instrumental. According to a report by McKinsey, predictive maintenance can reduce unplanned downtime by up to 40%, translating to significant savings in both time and money. By utilizing advanced monitoring technologies and data analytics, companies can identify potential issues before they escalate into costly breakdowns.
In a hydraulic system, wear and tear are inevitable, but traditional maintenance schedules often lead to either excessive servicing or neglected components. The application of predictive maintenance shifts this paradigm by utilizing real-time data from sensors and IoT devices. The global market for predictive maintenance is expected to reach $23.5 billion by 2024, indicating a robust adoption of these technologies. As reported by MarketsandMarkets, industries that implement data-driven predictive maintenance strategies can expect a 10-20% reduction in maintenance costs and a notable increase in equipment lifespan.
Furthermore, the integration of machine learning models allows for continuous improvement in maintenance strategies. These models can analyze historical data trends to predict failures more accurately and suggest optimal maintenance schedules. As industry players continue to adopt these innovations in hydraulic pumps, the potential for enhanced efficiency and sustainability becomes increasingly achievable, aligning with broader initiatives to reduce energy consumption and environmental impacts in industrial operations.
The Shift Towards Biodegradable Fluids: Enhancing Safety and Environmental Friendliness in Hydraulic Applications
The shift towards biodegradable fluids in hydraulic applications is gaining momentum, driven by an increasing awareness of environmental sustainability. According to a recent report by the International Journal of Hydraulic Engineering, the global hydraulic fluids market is projected to reach approximately $57 billion by 2025, with a significant segment stemming from the demand for eco-friendly alternatives. Biodegradable fluids, typically derived from renewable resources, offer a promising solution for reducing environmental impact while maintaining operational efficiency.
These innovative fluids not only enhance the safety profile of hydraulic systems but also mitigate the risk of contamination in case of leaks or spills. A study published by the Society of Automotive Engineers indicated that the use of biodegradable hydraulic fluids can lower ecological toxicity by up to 90% compared to conventional petroleum-based options. This statistic underscores the potential for these fluids to transform industrial practices, aligning with regulatory pressures and corporate sustainability goals.
Furthermore, advancements in formulation technology have led to biodegradable fluids that match or exceed the performance characteristics of traditional oils. Enhanced lubricity, thermal stability, and oxidation resistance are critical factors that industries rely upon for their hydraulic systems. Research from the American Society of Mechanical Engineers highlights that over 60% of companies are considering the switch to biodegradable options, reflecting a broader commitment to sustainable manufacturing practices. As industries pivot towards greener solutions, the adoption of biodegradable hydraulic fluids is poised to redefine efficiency and environmental responsibility in hydraulic applications.